Jet engines are one of the most jaw-dropping feats of engineering humans have ever come up with.
But jet engines shouldn’t be possible, says Ben Beake, director of materials research at Micro Materials, an equipment testing company in Wales.
“The air coming in is hotter than the melting point of the metal underneath, which is obviously not a good thing,” he explains, pointing out that this air reaches temperatures well above 1,000 °C.
Designers of jet engines have gotten around this problem by applying heat-resistant ceramic coatings to the engine blades. And now, researchers are developing yet stronger coatings that allow the engines to run hotter still.
“If you get it to go hotter, then there’s a massive saving on fuel and CO2,” says Dr. Beake. By increasing the temperature by just 30 °C or so, you might get an 8% fuel savings, he estimates.
Dr. Beake and his colleagues are tasked with pushing coatings to their limits in order to see how robust or effective they really are. His clients don’t always get the results they want. He recalls telling a missile manufacturer, “We’ve broken your coating,” some years ago. “They stormed off in a huff,” says Dr. Beake.
Besides exposing coatings to high temperatures, Micro Materials also has a “woodpecker” device, a tiny diamond stylus, which repeatedly taps a coating at random locations to test its durability.
Recently, the firm has worked with UK-based Teer Coatings to test a product that could be applied to satellite components, including gears and bearings used in various moving parts.
It is a tricky task, says Xiaoling Zhang from the company, because the coating must protect such components both pre-launch (when they are exposed to atmospheric humidity at ground level) and also in orbit, against dust particles and radiation in space. However, she claims that the firm has achieved the desired results.
But besides protecting spacecraft, coatings could also stop astronauts from getting sick.
Biofilms—gloopy accumulations of bacteria inside pipes – grow faster in low-gravity environments, which could be a problem for water supplies or machinery that moves fluid around on space stations or future spacecraft, for example.
“Biofilms are known to cause mechanical failures,” says Kripa Varanasi at the Massachusetts Institute of Technology. “You don’t want this.”
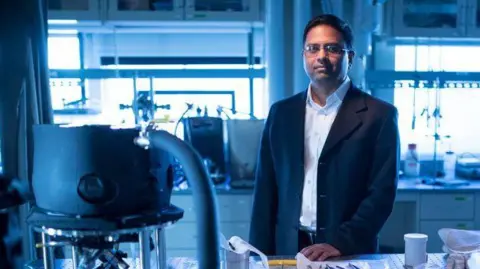
Prof. Varanasi and his colleagues have developed a range of coatings that make surfaces slippery and therefore resistant to the formation of biofilms. Tests of one such coating in an experiment carried out on board the International Space Station found that it worked as intended.
The idea behind the coating is to mix together a solid material and a lubricant. This is then sprayed onto the interior of a pipe or tube, which makes that inner surface extremely slippery.
Prof. Varanasi has previously made headlines for developing similar coatings for the insides of toothpaste packets—so you can get every last bit of toothpaste out. He and his colleagues have commercialised the technology through their spin-out company, LiquiGlide.
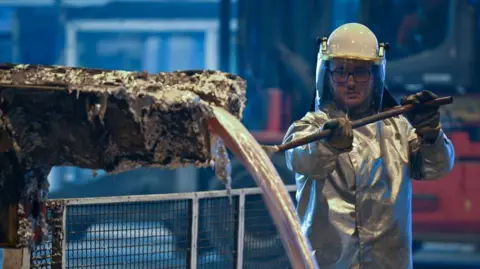
Slipperiness is, perhaps, an underappreciated attribute. Nuria Espallargas at the Norwegian University of Science and Technology and colleagues have developed a silicon carbide-based coating for equipment used in aluminium manufacturing or repair.
It is a sort of non-stick frying pan solution, meaning that layers of molten aluminium do not get stuck on this expensive equipment. The precise functioning of this particular coating is currently something of a mystery, though.
“To be honest, we really don’t know how it works; the mechanism is unknown at the moment,” says Prof. Espallargas.
Nonetheless, the coating is available commercially through her spin-out company, Seram Coatings. Atlas Machine and Supply, a US firm that makes and repairs industrial machinery, has tried it out.
“The real benefit lies in extending the life of the tools and improving the quality of the products being produced,” says Jeremy Rydberg, chief innovation officer.
He says that, without the coating, Atlas must rebuild the roller tools it uses to work aluminium every two days. This costs $4.5m annually. But the new coating means that these tools last for a whole week, not just a couple of days, slashing those rebuild costs to around $1.3 million per year.

Coatings can do some amazing things, but they don’t always work as intended, notes Andy Hopkinson, managing director at Safinah Group, a firm that often gets called in to investigate when coatings go wrong.
“We’re seeing a lot of issues at the moment with car parks, where their passive fire protection system is peeling off,” he says, referring to the fire-resistant paint sometimes applied to concrete structures.
And his company has also found that coatings applied to commercial ships do not always prevent barnacles and other sea life from attaching themselves to the hull. This problem, known as biofouling, increases friction, meaning the ship’s engine must work harder and burn more fuel.
Despite the availability of coatings that promise to help, ship owners do not always choose the correct one for their vessel. That choice should depend on where the ship is sailing, how long it is due to be idle rather than in motion, and so on, says Dr. Hopkinson.
The cost of fixing issues like this can run into many thousands, or even millions of pounds. “Typically, paint costs between 1 and 2% of the project. The problem is, when it goes wrong, the costs become exponential,” says Mr. Hopkinson.
The researchers working in this field, though, say that there are still many opportunities to improve coatings and develop new ones that could drastically improve the performance of machines or infrastructure in the future.